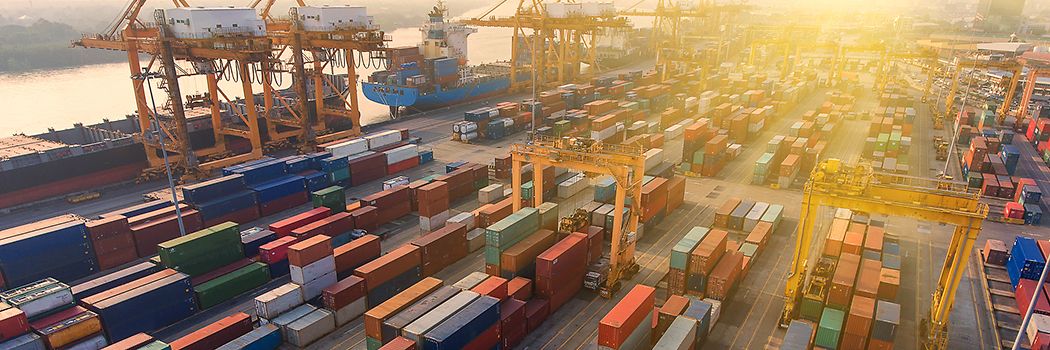
IoT in Transport und Logistik
Gestalten Sie jetzt die Lieferkette der Zukunft
Gestalten Sie jetzt die Lieferkette der Zukunft
Gestalten Sie jetzt die Lieferkette der Zukunft
Gestalten Sie jetzt die Lieferkette der Zukunft
ETA ist die Abkürzung für „Estimated Time of Arrival“, also die voraussichtliche Ankunftszeit. In der Logistik gibt der Absender dem Empfänger mithilfe der ETA eine Einschätzung, wann dieser mit der jeweiligen Lieferung rechnen kann. Bei der „Actual Time of Arrival” (ATA) handelt es sich dagegen um die tatsächliche Ankunftszeit, also eine konkretere Angabe. ETD steht für „Estimated Time of Departure“, die voraussichtliche Abfahrzeit. Dies kann der Zeitpunkt sein, wann eine Lieferung wahrscheinlich das Lager in Richtung Empfänger verlässt. Die Genauigkeit von ETA- und ETD-Angaben lässt sich unter anderem durch Tracking-Lösungen und digitale Wareneingangskontrolle – etwa mithilfe von elektronischen Frachtbriefen – verbessern: Denn so wissen Firmen immerzu, an welcher Stelle der Lieferkette sich die Sendung gerade befindet.
Smarte Logistik (engl. Smart Logistics) bezeichnet vernetzte und weitgehend automatisierte Logistik, die im Optimalfall sämtliche Unternehmen entlang der Wertschöpfungskette einschließt. Grundlage hierfür bilden digitale und intelligente Technologien wie das Internet of Things (IoT). Ein Ziel von smarter Logistik ist optimale Transparenz im Rahmen der Supply Chain, indem zum Beispiel Tracking-Lösungen Waren durchgehend nachverfolgbar machen. Zudem sollen Arbeitsprozesse so effizient wie möglich ablaufen: Pick-by-Vision und andere smarte Kommissioniermethoden unterstützen die Angestellten im Lager und erlauben ihnen, mehr Aufträge in kürzerer Zeit mit größerer Genauigkeit abzuwickeln. Der Begriff smarte Logistik fällt häufig im Zusammenhang mit der Bezeichnung Industrie 4.0, denn beide Konzepte ergänzen sich.
Im Internet of Things lassen sich Waren und Maschinen entlang der gesamten Lieferkette miteinander vernetzen. IoT-Tracker machen zum Beispiel Güter und Transportfahrzeuge nachverfolgbar, intelligente Lagersysteme erfassen Warenein- und -ausgänge automatisch, sodass Unternehmen stets einen transparenten Überblick über ihren Bestand und Sendungen haben. Indem IoT-Sensoren Nutzungsdaten von Maschinen und Fahrzeugen analysieren und bereitstellen, können Betriebe zudem Wartungszyklen vorausplanen und möglichst lückenlose Prozesse sicherstellen.
Der Begriff Logistik 4.0 ist eng verwandt mit der Bezeichnung smarte Logistik oder Smart Logistics. Ähnlich wie bei der Industrie 4.0 bezieht sich die Zahl auf die vierte industrielle Revolution. Sie folgt unter anderem auf die erste industrielle Revolution, die Ende des 18. Jahrhunderts begann und die wirtschaftliche Arbeit mit Dampfmaschine & Co. neu definierte. In der Logistik 4.0 ist es in erster Linie digitale Technologie, die Betriebsabläufe revolutioniert: Lösungen wie künstliche Intelligenz (KI) und das Internet of Things (IoT) schaffen optimale Transparenz entlang der Supply Chain, vernetzen Waren, Maschinen sowie Mitarbeitende und ermöglichen automatisierte Prozesse. Sensoren und andere Hardware generieren Daten, die Unternehmen nutzen können, um ihre Effizienz und Wettbewerbsfähigkeit zu steigern.
Logistik 4.0 bietet unter anderem folgende Vorzüge:
Diese und weitere Möglichkeiten der Logistik 4.0 helfen Betrieben dabei, auf dem umkämpften Markt zu bestehen.
Track and Trace ist die englische Bezeichnung für Sendungs- oder Warenverfolgung. Wenn versendete Güter oder auch Transportfahrzeuge mit Trackern ausgestattet sind, können sowohl Empfänger als auch Absender nahezu in Echtzeit jederzeit feststellen, wo sich die entsprechenden Objekte befinden – ob sie zum Beispiel in einem Stau stehen, bereits in einem Frachthafen oder auch im Lager am Zielort eingetroffen sind. Die Lokalisierung ermöglichen dabei verschiedene Funktechnologien wie NarrowBand IoT (NB-IoT), klassischer Mobilfunk oder WLAN. Durch Temperaturfühler und andere smarte Sensoren lässt sich das Track-and-Trace-Prinzip unter anderem um Condition-Monitoring-Systeme erweitern: So behalten Betriebe beispielsweise den Zustand von sensiblen oder verderblichen Waren wie Lebensmitteln und Medikamenten im Auge. Zusammengenommen ermöglicht Track and Trace unter anderem eine bessere Liefertreue, einfache Schadensfeststellung für Versicherungen und optimale Planung von Arbeitsprozessen, da sich Ankunftszeiten genauer voraussagen lassen.
Last Mile Delivery bezieht sich auf die sogenannte “letzte Meile“ einer Lieferung, also die finale Auslieferung der Ware an den Empfänger. Obwohl diese Phase oft die kleinste Distanz im Rahmen der gesamten Lieferkette umfasst, stellt sie Logistikunternehmen häufig vor besondere Herausforderungen. Denn wenn es auf der letzten Meile zu Verzögerungen kommt, warten alle nachfolgenden Empfänger länger auf ihre Bestellung, was die Customer Experience trübt. Digitale Technologie kann Transportunternehmen schon heute bei der Last Mile Delivery unter die Arme greifen: Zum Beispiel mit portablen Computern (Handhelds) oder Smartphones, die Fahrern den optimalen Weg zum Ziel anzeigen und dynamische Routenplanung ermöglichen. In Zukunft könnten weitere Innovationen die letzte Meile transformieren, etwa in Form von Drohnen, die direkt zum Empfänger fliegen und so den Verkehr umgehen.
Beacons (dt. Leuchtfeuer) sind Funkeinheiten, die drahtlos – zum Beispiel via Bluetooth Low Energy (BLE) – Informationen an Empfangsgeräte im nahen Umfeld senden. Bei diesen Empfängern kann es sich um Smartphones, Tablets oder Smart Devices wie Wearables handeln. In der Industrie 4.0 optimieren Beacons zahlreiche Prozesse, und auch in der Logistik lassen sie sich gewinnbringend einsetzen. Wenn Unternehmen Beacons beispielsweise an Paletten, Maschinen oder Gütern im Lager anbringen und die Smartphones ihrer Angestellten mit entsprechenden Apps ausstatten, nehmen die Mobiltelefone automatisch die Signale von Beacons in der Nähe auf – etwa Standortinformationen. In Verbindung mit einer entsprechenden Cloud-Plattform lassen sich diese Daten auf verschiedene Arten nutzen: Beschäftigte wissen zum Beispiel stets, wo sich welches Objekt befindet und vermeiden langes Suchen, was die Effizienz steigert. Auch den Warenfluss innerhalb des Unternehmens oder Lagers können Betriebe so besser nachvollziehen und so Lauf-, Transportwege und Prozesse optimieren. Der Bestand lässt sich ebenfalls leicht feststellen, da klar ist, wie viel Ware im Lager vorhanden ist. Nicht zuletzt können Beacons zusammen mit passender Software auch als Ersatz für die traditionelle Stempeluhr fungieren: Indem Sie mit den mobilen Geräten der Angestellten bei deren Betreten oder Verlassen des Betriebs kommunizieren, lassen sich Arbeitszeiten automatisiert feststellen.
IoT-Sensoren sind Geräte, die bestimmte Parameter erfassen und diese Informationen in eine Cloud übermitteln. Je nach Anwendungsfall eignen sich unterschiedliche Typen von IoT-Sensoren: Einer der wichtigsten Use Cases in der Logistik sind Positionstracker, die den Standort von Waren oder Transportmitteln bestimmen und so Transparenz entlang der Lieferkette schaffen. Temperaturfühler registrieren hingegen, wie warm oder kalt es in ihrem Umfeld ist. So können Logistikunternehmen sicherstellen, dass die Kühlkette bei Lebensmittel- oder Medikamententransporten eingehalten wird. Kipp- und Stoßindikatoren erfassen unterdessen Neigungen oder ruckartige Bewegungen. Kommt es aufgrund dessen zu einem Schaden an der Ware und können Betriebe dank der Sensordaten nachweisen, wie es zu der Beschädigung gekommen ist, erleichtert dies die Schadensregulierung mit der Versicherung.
Remote Maintenance meint die Wartung aus der Ferne. Voraussetzung ist die Vernetzung der Maschinen und Geräte, die zu warten sind. Ein Logistikbetrieb könnte also zum Beispiel seine Lagerroboter vernetzen und viele Defekte mittels Remote Maintenance schnell beheben, ohne, dass ein Techniker direkt vor Ort sein muss.
Pick-by-Vision ist eine smarte Kommissioniermethode, bei der Lagerangestellte alle Informationen zu Aufträgen über eine Datenbrille erhalten. Das Prinzip dahinter wird als Augmented Reality bezeichnet, weil virtuelle Daten die Realität der Beschäftigten anreichern. Pick-by-Vision bietet zahlreiche Vorzüge. Zum Beispiel können Angestellte effizienter arbeiten, da sie beide Hände frei haben. So sind sie in der Lage, mehr Aufträge in kürzerer Zeit abzuarbeiten, was Unternehmen in der kompetitiven Logistikbranche einen wertvollen Vorteil gegenüber der Konkurrenz verschaffen kann. Daneben können Firmen durch Pick-by-Vision auch ihre Nachhaltigkeit steigern, weil das System die notwendigen Informationen digital bereitstellt und weniger Papiermüll anfällt.
Smarte Kommissionierung ist integraler Bestandteil smarter Logistik und Logistik 4.0. Dabei nutzen Beschäftigte im Lager digitale Technologie, um effizienter und zuverlässiger zu arbeiten. Statt beispielsweise mit handschriftlich ausgefüllten Auftragszetteln oder Lieferscheinen zu hantieren, erhalten sie alle wichtigen Informationen am Point of Use über Sprachbefehle (Pick-by-Voice), LED-Anzeigen (Pick-by-Light), Datenbrillen (Pick-by-Vision) oder andere smarte Kommissioniermethoden.